

Shipboard Pollution Control: U.S. Navy Compliance with MARPOL Annex V (1996)
Chapter: 7 waste handling on submarines, waste handling on submarines.
The U.S. submarine force is composed largely of attack submarines (SSNs) and ballistic missile submarines (SSBNs), along with a few research submarines. The current fleet is described in Table 7.1 . Many of the 637s will be decommissioned in the next 13 years. The Seawolf class is apparently complete, and no firm date has been established for commissioning the new class (NSSN).
All U.S. submarines are nuclear-powered and have the ability to stay submerged for entire missions lasting up to several months. Control of the ship's atmosphere is very important. Unlike surface ships, submarines are almost never resupplied at sea. They begin their patrol with a full load of foodstuffs and other supplies adequate for the crew. The limited available space in a submarine means that all unnecessary packaging material must be eliminated. Cardboard boxes are unpacked, and the cardboard is left at the dock. Many of the foodstuffs come in metal cans. Syrups are usually used for mixing soft drinks. Many spare parts are partially unpacked before being stored aboard.
Waste that is discharged overboard must either be pumped out against the ambient sea pressure or blown out using pressurized air. Waste materials are collected and periodically discharged. The potential impact on ship safety associated with opening valves to the sea and on ship detectability by running pumps or blowing tanks to the sea makes waste disposal operations a significant event. Mission considerations may force waste disposal operations to be suspended for some period of time.
Dry waste is consolidated using a trash compactor and then placed in special cans. These cans are fabricated on board from prepunched galvanized, perforated steel sheets, using a roller tool. The resulting cans are 28.5 inches long and 9 inches in diameter. They have metal tops and bottom caps. Metal weights are added to ensure that the cans will go to the bottom. The cans are ejected from the submarine using a trash disposal unit (TDU), which is a long cylindrical, vertical tube connected to the ocean through a ball valve. Several cans are placed atop one another in the TDU, the top of the TDU is sealed by closing a pressure cap, the ball valve is opened, and the cans ejected through a combination of gravity and air pressure.
Table 7.1 Major U.S. Submarine Classes
Submarine waste streams differ in some respects from the waste generated by surface ships. Table 7.2 gives Navy data obtained from brief surveys taken on two submarines. Surface ship waste generation data are included for comparison. The differences in the numbers are impressive. One must suppose that there is submarine-to-submarine variation that is substantial, but the accuracy of the data is probably not high. The data do support the diligent job the submariners have done in reducing unnecessary packaging materials.
It has been suggested that the cardboard portion (0.10 and 0.50, for the two submarines) is not discharged, but stored on board. With present practice, the weight of the metal TDU cans (including metal weights), which ranges from 0.26 to 0.61 lb/person/day, must be added to the submarine waste streams. These additional TDU metal weights are not included in Table 7.2 , since they have no counterpart in the surface fleet and result solely from the current submarine discharge process. The data suggest that a storage volume as low as 0.01 ft 3 /person/day would be necessary to accommodate this waste if it is not discharged. This assumes a compaction ratio for the total waste stream of about 15, which is commercially obtainable.
Another important result of the shipboard surveys is that a substantial portion of the paper and plastic (but not the cardboard, metal, and glass) is food contaminated ( Table 7.3 ). The compacted volume of the food-contaminated paper and plastic is not very large, less than 0.01 ft 3 /person/day, or about 1 ft 3 /day for the entire ship. If this waste cannot be eliminated and has to be stored under Annex V, storage in the frozen food lockers appears to be the only solution. Precautions to avoid contamination of unused supplies will be necessary.
Since submarines operate as closed systems leaving port with everything they will use aboard, an argument can be made that there is space to continue storing the Annex V waste rather than discharge it through the TDU. The waste-handling study (U.S. Navy, 1994) for the new design NSSN concluded that proper management of the solid waste stream could allow storage and eliminate any waste discharges. Again, food-contaminated waste materials would need special handling, probably storage in sealed cans held in the frozen food lockers. There appears to be a strong conservation ethic among submariners, and a number of crews have already voluntarily made significant reductions in the amount of solid waste discharged.
The consensus of the committee is that there are no technological solutions to the submarine waste problem beyond installation of garbage disposals, better compactors, and sealed storage packages. Thermal destruction in the submarine environment is not appealing. Further, the committee sees no route to an integrated solution to the larger waste problem going beyond Annex V. Submarines generate food waste, gray water, and black water in proportion to the complement. Present storage and discharge strategies have not been improved upon by committee deliberation. The submariners have done an excellent job on their own.
Table 7.2 Rate of Generation of Annex V Solid Waste (lb/person/day)
Table 7.3 Rate of Generation of Contaminated and Noncontaminated Paper and Plastic Waste (lb/person/day)
READ FREE ONLINE
Welcome to OpenBook!
You're looking at OpenBook, NAP.edu's online reading room since 1999. Based on feedback from you, our users, we've made some improvements that make it easier than ever to read thousands of publications on our website.
Do you want to take a quick tour of the OpenBook's features?
Show this book's table of contents , where you can jump to any chapter by name.
...or use these buttons to go back to the previous chapter or skip to the next one.
Jump up to the previous page or down to the next one. Also, you can type in a page number and press Enter to go directly to that page in the book.
Switch between the Original Pages , where you can read the report as it appeared in print, and Text Pages for the web version, where you can highlight and search the text.
To search the entire text of this book, type in your search term here and press Enter .
Share a link to this book page on your preferred social network or via email.
View our suggested citation for this chapter.
Ready to take your reading offline? Click here to buy this book in print or download it as a free PDF, if available.
Get Email Updates
Do you enjoy reading reports from the Academies online for free ? Sign up for email notifications and we'll let you know about new publications in your areas of interest when they're released.
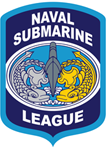
NUCLEAR SUBMARINE DISPOSAL AND RECYCLING
The following paper ls an excerpt from the booklet U.S. Naval Nuclear Powered Submarine Inactivation. Disposal. and Recycling published In March of 1995 by the Sea Systems Command of the U.S. Navy. 1he information from that publication is reprinted in response to several requests for the rest of the story following Mr. Bill Galvani’s article Mooring ALPBA-End of the line in the October 1997 SUBMARINE REVIEW. Minor statistical revision has been done In updating the number of reactor compartments transported from Puget Sound Naval Shipyard to the Department of Energy’s Hanford Site.
Navy ships are inactivated at the end of their useful lifetime when their military capability does not justify the cost of continued operation, or when necessary to comply with treaty requirements that limit ballistic missile capacity. When the decision is made to inactivate a nuclear powered submarine, it must be defueled, and appropriate actions must be taken to dispose of the reactor plant and the remainder of the submarine.
In the late 1970s the Navy recognized that a number of nuclear powered submarines would require inactivation and disposal in the coming years. In accordance with the National Environmental Policy Act, the Navy began evaluating alternatives for disposal. Two basic options were evaluated: 1. Disposal of the defueled reactor compartment (the section of the submarine containing the reactor plant) at an existing land burial site, with the non-radioactive remainder of the submarine disposed of either by sinking at-sea or by cutting up for sale as scrap metal; or 2. Disposal by sinking the entire defueled submarine in the deep ocean.The Navy’s 1984 Final Environmental Impact Statement found that either land or sea disposal of the reactor compartments would be environmentally safe and feasible. The Record of Decision issued by the Navy on December 6, 1984, concluded that Based on consideration of all current factors bearing on a disposal action of this kind contemplated, the Navy has decided to proceed with disposal of the reactor compartments by land burial. As of April 1, 1998 the Navy ha, safely shipped 73 submarine reactor compartments to the Department of Energy’s disposal grounds at Hanford, Washington.
Initially, the forward and aft sections of the defueled and decommissioned submarines were rejoined and placed in floating storage following reactor compartment removal, while a permanent program was being developed to eliminate the remainder of the ship. In 1991 the Navy began to recycle these rejoined submarine sections. Currently, recycling these sections of the submarine is accomplished in parallel with the reactor compartment removal work. The recycling process removes and refurbishes components having value to the Navy and cuts apart the remainder of the submarine to allow segregation and recycling of metals and other materials of value.
The submarine disposal operations developed by the Navy do not involve any sophisticated technology, but use basic engineering principles and common industrial practices. From the outset, the major program goals were minimizing radiation exposure, meeting state and federal environmental and safety regulations, and controlling cost. The technology to perform submarine inactivation and recycling is straightforward and well within the capability of a large shipyard. It is basic disassembly, component removal, heavy lifting, packaging, and transporting, which are comparable to ship construction and repair activities. The most time consuming actions are those needed to meet regulatory requirements common to the disposal of all U.S. warships, such as removal of chemical residues from metal surfaces.
Submarine inactivation and disposal work employs the same safety and environmental controls that are used for work on nuclear powered ships undergoing overhaul. Work involving radioactivity, lead, asbestos, PCBs, or other hazardous materials, is accomplished by personnel trained to work with these materials. They are equipped with the proper personal protective equipment where needed, and the work is accomplished in areas that are controlled to prevent the spread of contaminants. Waste is controlled and disposed of in accordance with applicable state and federal regulations, using licensed transportation contractors and approved disposal sites.
The control of radiation exposure to shipyard workers is discussed in detail in the Navy’s annual report NT-98-2 of February 1998. This report shows that the average occupational exposure of each person monitored in the shipyard workforce is less than two-tenths of a rem per year. For comparison, the amount of radiation exposure a typical person in the United States receives each year from natural background radiation is three-tenths of a rem. Individual worker exposure is strictly controlled, resulting in exposures less than 50 percent of the federally established limit of 5 rem per year. In fact, no shipyard worker has exceeded 2 rem in any given year since 1979.
Inactivation
Submarines scheduled for inactivation have their weapons removed prior to arrival at the shipyard. Upon arrival, the submarine’s reactor is shut down and the submarine is inactivated and defueled in a planned sequence. Expendable materials, technical manuals, tools, spare parts, and loose furnishings are removed, including items such as linen, kitchen supplies, and utensils. Classified/sensitive equipment and materials including the cryptographic facilities are removed. The main storage battery is removed from the submarine. Refrigerant and oxygen are offloaded. Piping for sea water, main steam, potable water, fuel oil, and other systems not needed for defueling operations are drained. Hydraulic system are drained and flushed. Tanks containing fuel oil and other fluids are drained and cleaned. Sanitary systems are drained, cleaned, and disinfected. The submarine’s electrical and lighting systems are de-energized and temporary ventilation, lighting, power, and compressed air services are installed.
With the ship in drydock, an opening is cut in the hull, interferences are removed, and a refueling enclosure is installed on the hull over the reactor to provide a controlled work area with filtered ventilation. Access is provided into the reactor and fuel is removed into a shielded transfer container which is then moved by crane to a dockside enclosure. The fuel is placed into a specially-designed shipping container. Defueling employs the same proven procedures and equipment that have been successfully used in over 300 naval rector refuelings and defuelings.
After defueling, preparations are made to facilitate reactor compartment removal. The pressure vessel, piping, tanks, and fluid system components that will remain with the reactor compartment are drained to the maximum extent practicable, while keeping radiation exposure to workers as low as reasonably achievable. Absorbent is added to the accessible internal areas to fix in the absorbent residual liquid that may be present. The system draining procedures are effective in removing nearly all (over 98 percent) of the liquid originally present. Only a small amount of liquid remains trapped in discrete locations such as pockets in valves, pumps, tanks, vessels, and other inaccessible piping system components. All openings into radioactive systems are sealed. At this point the rector compartment is ready to be separated from the submarine and packaged for disposal.
Missile Compartment Dismantlement
In 1980, because of SALT II Treaty limits, the Navy began retiring ballistic missile submarines. Under the terms of the treaty, the missile launchers were required to be removed from the submarine and cut apart in a verifiable manner. For the first submarines, the submarine was inactivated and the missile compartment section of the submarine was dismantled using cutting torches. The remaining forward and aft sections of the ship were welded together and placed in floating storage. After the initiation of reactor compartment disposals at Puget Sound Naval Shipyard in the mid 1980s, the missile compartments were dismantled in parallel with removal of the reactor compartment. The remaining sections of the submarine were welded back together and the ship was placed in waterborne storage. With the initiation of total ship recycling in 1991, Puget Sound Naval Shipyard began accomplishing missile compartment dismantlement, reactor compartment removal, and ship recycling in a single drydocking evolution.
Missile compartment dismantlement employs the same cleaning, cutting, and removal methods used for dismantling the rest of the submarine. The missile batches and the missile launcher tube liners are removed. The interior spaces are cleared to allow the bull to be cut apart. The hull and missile tube structure is dismantled using cutting torches. Equipment within the missile compartment removed prior to and during dismantlement, includes electrical equipment, piping, air flasks, lockers, partitions, and berthing furnishings. Where required, components are demilitarized to remove sensitive or classified design information, PCB impregnated sound damping material is removed and the residue is cleaned from exposed surfaces. Asbestos insulating material and removable ballast lead are manually taken from the ship.
Reactor Compartment Disposal
The nuclear propulsion plants in U.S. Navy ships, while differing somewhat in size and component arrangements, are all rugged, compact, pressurized water reactor plants designed to exacting criteria in order to withstand severe power transients and battle shock. These compact plant designs, enclosed within the high strength steel bull of the submarine, tend to simplify disposal planning (as compared to large spread out land based nuclear power plants).
The defueling process removes the nuclear fuel, including unused uranium and fission products which are fully contained within the fuel elements. Although this removes over 99 percent of the radioactivity. some small amount remains in the reactor plant after the nuclear fuel is removed. This radioactivity was created by neutron irradiation of the iron and alloying elements in the metal components during operation of the plant. Approximately 99.9 percent of the remaining 1 percent radioactivity is radioactive corrosion and wear products which have been deposited on the inside of piping systems.
Cobalt 60, which has a half life of S.27 years, is the dominant residual radioactive nuclide. It emits gamma radiation and is the primary source of radiation in the defueled reactor plant during reactor compartment preparation and shipment to the burial site. Experience shows the external radiation levels on the reactor compartments are low-below 1 mrem per hour at the bull surface except for one or two localized which do not exceed 30 mrem per hour. These levels drop to 1 mrem per hour or less at two meters distance from the hull. The radioactive corrosion and wear products are contained within two boundaries, the first being the sealed piping systems, and the second the welded hull and bulk-heads of the reactor compartment.
The planning for reactor compartment disposal began in the late 1970s, and evolved in the early 1980s into a comprehensive public process under the National Environmental Policy Act. The Navy, with the Department of Energy as a cooperating agency, published a draft Environmental Impact Statement (EIS) discussing alternatives in 1982. Public hearings were held in four states: North Carolina, South Carolina, California, and Washington. Copies of the draft EIS were made widely available. Over 1000 comments were received in the public hearings and comment letters. The final EIS, published in 1984, concluded that land burial of submarine reactor compartments at a federal government disposal site would not have any significant adverse environmental impact. On December 6, 1984, the Navy issued a Record of Decision to dispose of these reactor compartments at the Department of Energy’s Hanford Site in eastern Washington.
The Hanford Site was selected because it was close to a navigable river, in a desert, and relatively close to Puget Sound Naval Shipyard where eight defueled submarines were already in floating storage. The other federal radioactive waste disposal sites did not have these combined features. Shortly after the Record of Decision was issued, the 1985 Low Level Radioactive Waste Policy Amendment Act became law, which identifies disposal of reactor compartments from naval ships to be a federal responsibility.
Reactor compartments also contain regulated quantities of hazardous and toxic materials in the form of lead and PCBs. The lead is in the form of permanently installed shielding which is not removed because of the great difficulty and significant personnel radiation exposure that would be involved. Felt sound-damping material containing PCBs is found on the interior of the bull, on bulkheads, and in other locations outside of the reactor compartment that are pan of the disposal package. This material and any PCB residue are removed from the reactor compartment before disposal in accordance with EPA requirements. However, low concentrations of PCBs, totaling about five pounds, are found tightly bound in the chemical composition of rubber and insulating materials widely distributed throughout the reactor compartment. It is not feasible to remove these components and insulation, and they are left in place for disposal with the reactor compartment.
Reactor compartments are prepared for shipment and burial in accordance with Department of Transportation and Nuclear Regulatory Commission requirements for packaging and transportation of low level radioactive material, Department of Energy requirements for burial of low level radioactive material, Environmental Protection Agency requirements for disposal of PCBs, and Washington State Department of Ecology requirements for disposal of lead.
Because of their radioactive content, the reactor compartment packages are designed to meet the packaging requirements of Title 49 Code of Federal Regulations-Transportation. and Title 10 Code of Federal Regulations-Energy. The reactor compartment packages will effectively protect the public and environment when subjected to normal conditions of transport as well as hypothetical conditions relating to beat, cold, pressure, vibration, drop, and puncture. The potential damage to the reactor compartment and its contents under the hypothetical accident conditions has been shown to not exceed specified limits for release of radioactivity.
When performing the reactor compartment shipments, the Navy has maintained close coordination with state and local officials. In 1986, Navy, Coast Guard, and Department of Energy officials met in olympia, Washington, with representatives of the Washington State Department of Ecology, the Washington State Office of Radiation Protection, and the Nez Perce and Yakama Indian Nations, to review preparations for the first reactor compartment shipment.
Officials of the states of Washington and Oregon have been to the shipyard to review the transport barge and reactor compartment packages and to confirm the packages radiation levels. This close coordination provides continuing assurance to the states and the public that these shipments meet all of the necessary requirements for transporting radioactive material, and do not represent a danger.
In preparation fur removal of the reactor compartment from the ship, piping, electrical cabling, and other components that penetrate the reactor compartment bulkheads, or would otherwise interfere with its removal, are cut and removed. This work is accomplished with hand held saws, grinders, pipe cutters, and cutting torches. Special care is taken with piping containing radioactivity. These are high integrity systems designed to prevent any leakage. Any pipes which are cut are resealed to maintain the system integrity and, in combination with the package hull and bulkheads, provide redundant boundary containment of radioactivity. PCB-bearing felt is manually removed and the surfaces cleaned either by abrasive blasting or by hand scraping and wire brushing, followed, in some cases, by wiping with chemical and detergent rinses. Ballast lead is manually removed.
The ship drydocked with the reactor compartment supported by cradles. Tracks with rollers are installed under the cradles to allow the reactor compartment to be slid away from the ship once it is cut free. The reactor compartment is cut from the rest of the ship’s structure with standard cutting equipment, predominantly torches and hand held saws, pipe cutters, and grinders. The bull cuts are made several feet forward and aft of the shielded reactor compartment to allow installation of shipyard fabricated end bulkheads. These are three quarter inch thick steel plates with heavy T-beam stiffeners. These plates are transported to the drydock, crane lifted into position, and welded into place after the reactor compartment is moved away from the rest of the submarine.
These submarines were designed for deep ocean operations and to survive combat engagements. Thus, the rugged design of the submarine reactor plant, the inherent strength of the ship’s pressure hull and the shielded bulkheads, and the additional end bulkheads installed by the shipyard, provide the structural integrity needed to meet the packaging criteria for transporting the radioactive material contained in the reactor compartment. In addition, the entire package is air tested to insure package integrity. The shipyard also fabricates heavy steel support fixtures which are welded to the hull to facilitate jacking and transporting the reactor compartment. Jacking is accomplished in small increments, with blocks and shims placed under the compartments as they are raised to assure that the compartments do not drop in case of a loss of hydraulic jacking pressure.
The reactor compartment package moved onto the barge using track-mounted, high capacity rollers for horizontal movement, and large hydraulic jacks for vertical movement. When in place, the compartments are welded to the steel barge deck.
Reactor Compartment Transportataion
Barge shipment. The Navy reactor compartment shipments meet all Department of Transportation requirements for transportation of low level radioactive material. Beyond these requirements, the Navy employs additional conservative precautions designed to ensure safe shipment of the reactor compartments.
The barge is towed from the shipyard using a large commercial American Bureau of Shipping certified ocean tug. The tow is accompanied by a second, similar backup tug and a Navy or Coast Guard escort vessel. The route follows the normal shipping lanes from the shipyard, through Rieb Passage, past Restoration Point, and northerly through Puget Sound. The route is then westerly through the Strait of Juan De Fuca (staying in U.S. waters), past Cape Flattery, and southerly down the Washington coast to the mouth of the Columbia River (shipment departure times from the shipyard are calculated to allow passage across the bar at the mouth of the Columbia River on the incoming tide). The route is then up the Columbia River, following the Corps of Engineers maintained shipping channel used for the regular transport of commercial cargo. The ocean tugs are replaced with river tugs on the lower Columbia River. The river route passes through the navigation locks at the Bonneville, Dalles, John Day, and McNary dams, and finally to the Port of Benton located at Richland, Washington.
In addition to meeting Department of Transportation and U.S. Coast Guard requirements, the Navy takes extensive additional precaution to ensure the tow is safe and uneventful. Even though a barge accident is highly unlikely, credible scenarios have been analyzed. These analyses show there is no significant risk to the public or the environment.
The equipment and the transportation procedures are designed to minimize the potential for transportation accidents, to mitigate the consequences of an accident in the unlikely event one should occur, and to facilitate recovery if necessary. Care is taken to make barge accidents highly unlikely. For example, only experienced commercial towing contractors are used, with the advantage of employing people experienced in the work and the route, using regularly operated and maintained equipment. Two tugs are used, one for the tow and one traveling along as a backup to take over in case of a problem with the primary tug. Fully crewed, American Bureau of Shipping certified, commercial ocean tugs are specified for the two from the shipyard to the Columbia River. These vessels have more power than would be normally employed for a barge of the sil.e and load-line rating used for reactor compartment disposal. Large pusher-type river tugs and backups having reserve engine capacity are used on the Columbia River.
All towing operations, including the route to be followed, operating procedures, and casualty procedures, are planned by the towing contractor and approved by the Navy. Normal shipping lanes are used through Puget Sound to minimize the potential for collision or inadvertent grounding. The barge is equipped with flooding alarms. A backup towing bridle and tow line are installed on the barge with a trailing line behind the barge for bringing backup towing gear aboard the tug if the primary towing gear fails. Shipments are not made in the winter or when inclement weather is predicted. Shipments are also planned to avoid interfering with scheduled recreational events, such as boat races, on the low tide.
Licensed ship pilots are used in Puget Sound and on the Columbia River, and for crossing the Columbia River Bar. Shipyard personnel familiar with the towing procedures and the characteristics of the reactor compartment accompany each shipment to monitor the operations and provide advice to the tug captain if needed. Coast Guard personnel are also stationed aboard the escort vessel. With the above precautions, the potential for a towing accident involving the barge is much lower than the already small probability of accidents during routine barge traffic throughout the United States.
Each of the barges used is highly compartmented and is designed to maintain its upright stability with any two compartments flooded. The welds attaching the reactor compartment to the barge are designed to withstand the maximum forces associated with wind loading, list, trim, pitch, roll, yaw, and any credible accident. Also, the combined rector compartment and barge have sufficient reserve buoyancy to keep the barge afloat even if over half of the compartments were damaged and flooded. Therefore, a barge sinking would take an extremely unlikely accident scenario. Because the rector compartment sits well back from the sides of the barge and because the extremely strong exterior of the package can withstand severe accidents, breach of the reactor compartment due to collision is not considered a credible event.
Damage due to fire is also extremely unlikely. The transport barge carries no combustible fluids to support a fire. Also, the thick steel shell of the reactor compartment has a high capacity for absorbing heat and would not be damaged significantly if exposed to fire. In addition, the waterborne shipment environment would provide easy access to firefighting water to put the fire out.
There are no other credible accidents related to water transportation that could cause breach of the package and release of radioactivity. In the highly unlikely event it became necessary, the Navy has incorporated in the barge and package a number of engineered features to facilitate location and salvage. A buoy is attached to the barge and would float to the surface to mark its location. An emergency position indicating radio beacon would float to the surface and transmit a locating signal on a frequency monitored by the National Transportation Safety Board. Salvage capability is provided for the package to allow the attachment of salvage gear to raise the sunken reactor compartment package using commercial or Navy owned heavy lift ships if refloating the barge is not possible. The barge and package could be raised as a unit, or separated by divers for separate recovery, without any impact on the environment.
offloading and land transportation. Offtloading is accomplished at the Port of Benton at Richland, Washington. Facilities at the Port consist of a barge offloading slip constructed of sheetpiling cofferdams and rip-rap earthen bulkheads. The slip is periodically inspected both above and below water to ensure it is in good condition. Maintenance work is controlled under the provisions of an Army Corps of Engineers permit, and state and local permits and authorizations which are designed to protect river quality.
Before the barge is docked, divers inspect the slip to assure the gravel bottom is free of obstructions. The barge is placed in the slip and water is added to the barge compartments in a controlled sequence to ground the barge firmly on the gravel bottom of the slip, with the deck of the barge against and level with the top of the sill at the landward end of the slip.
The welds holding the reactor compartment package to the barge are cut, and the compartment is jacked up and placed upon four steel columns. A crane is not required for this work. As is done during dydock lifts, jacking is in small increments with support blocks and shims temporarily placed under the load to support the compartment if hydraulic jack pressure is lost. A transport vehicle is then moved onto the barge and under the package. The transport vehicle is commercially operated under contract. To date, these have all been multiple wheel high capacity trailers specially designed for heavy loads; however, high capacity crawler transport vehicles could also be used.
The package is attached to the transport vehicle using welded attachments, and raised off the support columns using jacking features built into the transport vehicle. The transporter is then driven off the barge, and the package transported approximately 26 miles to a burial trench at the Hanford Site. At the trench, the package is lowered onto foundations, the welded attachments to the transporter are cut free, and the transporter removed. The package is welded to the foundations.
The time from shipyard departure to placing the package in the trench is about five days, of which three days involve the barge transit. Potential offloading and land transportation accidents would all involve dropping or toppling the package, or collision with another vehicle. Because of the package design, none of these accidents has the potential to release radioactivity.
The potential for mishandling the package is minimized in a variety of ways. Offtloading and land transportation is accomplished under a Navy contract by commercial contractors experienced in handling heavy loads. Conservative engineering designs, load testing of equipment, the use of Navy approved written procedures. and independent monitoring of the work all minimize the potential for a problem. The transport vehicles that are used are designed to transport heavy loads and are very stable. The overland transit is coordinated by Hanford Site transportation personnel. Escort vehicles provide an escort and assure a clear roadway for the transporter. minimizing the potential for collision with other vehicles. The only train tracks along the route are located on the Hanford Site and used infrequently by trains transporting site materials at moderate speed.
Hanford is a 560 square mile (1450 square kilometers). mostly undisturbed area of relatively flat desert. The Columbia River flows through the northern part of the site. The Tri-Cities of Richland, Kennewick, and Pasco to the southeast is the nearest population center. About 376,000 people Jive within an 80 kilometer radius of the center of the Site according to the 1990 census.
From 1943 until very recently, Hanford was the location of DOE’s reactor and chemical separation facilities for the production of plutonium for use in nuclear weapons. The work at Hanford is now primarily directed toward decommissioning the production facilities, disposal of the wastes, and actions to remediate contamination that resulted from past operations.
The active Hanford Low Level Burial Grounds consist of eight burial ground sites that cover a total area of approximately 518 acres in the Site’s 200 East and 200 West areas. The 200 East Area is located near the center of the Hanford Site on a plateau about 700 feet above sea level, and contains reactor fuel chemical separation processing facilities and various waste management facilities. The reactor compartments are placed in the 218-E-128 burial ground, one of two active burial grounds in the 200 East Area. This burial ground is an active landfill which began receiving waste in 1967.
The program for total ship recycling was developed directly from experience gained in dismantling missile compartments. Similarly, the development of procedures for demilitarization and handling of hazardous materials evolved from the experience. In 1991, the Navy instituted a total ship recycling program following a review of options for disposal of the remainder of the submarines.
Disposal by sinking became impractical when the combined cost of demilitarization and hazardous material removal was added to the already significant cost of preparing the submarine for refloating, towing, and controlled sinking, and the cost of actually towing it to an authorized ocean location and sinking it.
General approach to recycling. There are two basic approaches that have been used to optimize in-dock submarine dismantlement. The first is to remove large sections of the ship’s bull with most of the adjacent structure piping, cabling, and equipment still attached. The removal is accomplished in a planned and controlled dismantlement sequence involving about 460 major individual sections of bull and structure (for a ballistic missile submarine). The submarine’s internals are stripped only to the extent necessary to allow hull sections and deck sections to be cut free. The removed sections are placed on a land transporter (usually a railcar or flat bed truck) and moved to a shipyard facility where they pm through a number of workstations to be processed into segregated recyclable materials and waste.
The second approach is to strip the interior of the submarine (except for some heavy machinery) including the removal of all hazardous materials. Then, the hull is cut into sections as in the first method. One advantage of this approach is that the ship’s interior can be stripped before docking, shortening the in-dock time. This has become an important factor, as the increasing number of ships being recycled can potentially be limited by the drydocks available for hull cutup and reactor compartment preparation work. The other advantage is that the intact hull provides a good environmental containment for hazardous material removal operations inside the ship, including abrasive blasting.
The recycling process currently being used is actually a combination of the two approaches. Sections of the ship that can be easily stripped pierside are being stripped. Sections that have substantial interferences or other features that make shipboard stripping difficult, are being cut out for dockside disassembly and processing.
The shipyard has dedicated a drydock to the recycling of submarines that have already been defueled. It is divided by a caisson that allows new bulls to be docked while work proceeds on others. A track system allows partially recycled bulls to be moved from the seaward end to the landward end to accommodate the new bulls, and allows the reactor compartments to be moved aside for preparation for shipment. This dock can handle about eight hulls per year. Other drydoclcs are used to dock one or more submarines for reactor defueling. In this case, after defueling, the reactor compartment is prepared fur disposal, and the remainder of the ship is recycled.
Shipboard dismantlement. There are a number of hazardous materials present in older submarines that need special controls for health, safety, environmental protection. However, most of these are present in relatively small quantities in discrete locations. The exceptions are asbestos, PCBs, and metallic lead which are present in significant quantities. Thus, one of the first actions when a submarine is recycled is to identify and tag equipment and structure that contain these materials. This includes shipboard testing to identify insulating materials (both on piping systems and on ship’s structure) that contain asbestos or PCBs. This identification program allows the proper personnel safety and environmental controls to be established for shipboard dismantlement and in the subsequent dockside handling, processing, and disposition of the removed materials.
In dismantling the submarine, care is taken to unbolt and remove equipment that will be refurbished and reused. However, the remaining non-reusable equipment, wiring, piping, and non-structural material is most efficiently removed by destructive processes. It is cut free using reciprocating saws, grinders, abrasive cutting wheels, hand held shears, plasma torches, and oxygen/Methyl Acetylene Propadiene mixture (MAPP) gas torches. The lighter materials are cut into pieces that can be manually loaded into large material handling containers.
The machinery in the aft section of the submarine requires considerably more work to remove than the lighter equipment and materials in the forward section. Much of this heavy equipment must be crane lifted, even when cut into pieces. Large holes are cut in the top and sides of the submarine’s hull to facilitate removal of material from the ship during the early phases of dismantlement. Material handling containers are either lowered into the ship or placed alongside where material can be placed into them. Larger equipment is moved under a hull cut where a crane can lift it out of the ship.
Electrical wires and cables are cut using both hydraulic and manually operated cable cutting shears. Larger diameter piping is cut with band-held abrasive cutting machines having wheels up to 12 inches in diameter. Smaller diameter piping is abrasive cut or sheared. Hand-held plasma cutting torches are also used on non-ferrous alloys. Light metal items such as partitions and ventilation ducts are sawed or abrasive cut. All removed materials are cut into sizes that can be manually placed into the material handling containers.
Insulating materials are manually removed and disposed of as waste. Asbestos is removed in isolated areas with controlled and filtered ventilation. The work is accomplished by personnel who are specially trained in asbestos work. They wear protective clothing and breathe filtered air. Procedures such as wetting are employed to minimize the amount of fibers that become airborne. The work areas are monitored to assure the air quality remains within prescribed limits. The waste material is bagged, identified, and disposed of in accordance with established requirements.
PCBs are encountered in significant concentrations in felt sound damping material. On early submarines this material is found throughout the ship. This damping material is installed under bolted metal plates against hull or machinery foundation structures. These are often covered with additional insulating materials. The covering plates and the impregnated felt are manually removed and disposed of as PCB waste. The work is done in controlled areas by personnel wearing protective equipment. Where entire interior areas of the hull are stripped and cleaned, high capacity steel abrasive blasting equipment is used to remove the PCB residue. The areas to be abrasive blasted are isolated from the rest of the ship and provided with controlled and filtered ventilation. Personnel wear full body protective clothing and are supplied with breathing air. The steel abrasive is recovered and reused. The PCB waste is packaged and disposed of in accordance with applicable requirements.
Lead ballast in the way of hull sectioning work is manually removed from the bilge pockets. The individual pieces generally weigh about 60 to 100 pounds.
The heavy steel hull and structural materials are cut with hand- held oxygen/MAPP gas torches capable of cutting hull material at speeds up to 18 inches per minute. Extremely thick components such as shafts are cut with an oxygen lance (a consumable metal tube containing metal filaments and fed by an oxygen supply).
The recycled metals are segregated by type: stainless steel, carbon steel, aluminum, monel, brass, cooper, etc. to the maximum extent practicable. The heavy steel bull and structural steels are loaded directly into commercial railcars. The other metals are placed into large metal boxes or shipyard gondola railcars and taken to the local Defense Reautilization Marketing Office (DRMO)facility. This scrap metal is sold using either a onetime sale contract, or a term contract, awarded to the highest bidders. Reusable equipment not needed by the Navy or Defense Department is sold to private bidders through the DRMO.
A typical recycling generates about 2,500,000 pounds of HY-80 steel, 600,000 pounds of steel, 20,000 pounds of sheet metal, 110,000 pounds of stainless steel, 8,000 pounds of galvanized steel, SS,000 pounds of aluminum, 250,000 pounds of brass/- bronze, 150,000 pounds of monel, 90,000 pounds of copper, 6,500 pounds of zinc, and up to 1,800,000 pounds of lead.
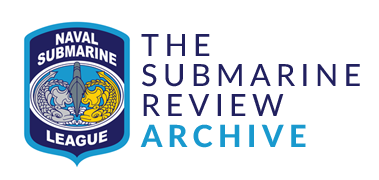
Naval Submarine League
- 405 N Henry St Alexandria, VA 22314
- (703) 256-0891
- [email protected]

Babcock begins recycling of its first decommissioned UK nuclear-powered submarine
Babcock international group (babcock), working with the defence nuclear enterprise (dne), has reached the next significant milestone to fully dismantle a nuclear-powered submarine, swiftsure, at its facility in rosyth..
Naval News Staff 12 Nov 2024
Babcock press release
As part of the UK’s demonstrator project, the company has recently awarded the recycling contract to KDC Veolia Decommissioning Services UK Ltd (KDCV). Babcock’s approach is a world first and will apply a new and innovative methodology which will enable around 90% of its structure and components to be reused or recycled. This includes the pressure hull around the reactor compartment, once full radiological reassurance monitoring has completed.
Swiftsure will be the first decommissioned UK nuclear-powered submarine to be fully dismantled and disposed of. It will lead the way, providing a proven approach for recycling of the current UK decommissioned fleet of submarines.
This milestone builds on work already completed by Babcock’s highly skilled teams to remove the submarine’s reactor systems and low-level radioactive waste. With safety and environmental protection at the centre of its operations, and using a specially designed in-dock facility, the waste has been processed for removal from site through Rosyth’s state-of-the-art active waste management facility.
Swiftsure remains on track to be dismantled by 2026, ahead of the wider programme to fully dismantle all decommissioned Royal Navy submarines, which will free up space and capacity that can be used in delivery of programmes enabling submarine availability.
Babcock Chief Executive, Nuclear, Harry Holt, said: “This is a world first. We are bringing together our experience of supporting the entire UK submarine fleet, our nuclear expertise and our ability to bring the best of industry together on this programme to spearhead the approach for the safe disposal of all ex-service nuclear submarines.”
“Working with the Ministry of Defence and Babcock on this unique and complex project will mark a new sustainable way of decommissioning and recycling this type of vessel. By using Veolia’s global skills, we will deliver this world-first project as part of our GreenUp strategic programme designed to depollute, decarbonise and preserve resources.” Veolia’s John Abraham, Chief Operating Officer – Industrial, Water & Energy for UK, Ireland and Nordics
To mark the official start of the hull dismantling, this month Babcock and the DNE welcomed more than 40 former crew members to bid Swiftsure a fond farewell, as Submarine Delivery Agency, Head of Disposal and Devonport Infrastructure, Chris Carpenter, made the first ceremonial cut of steel.
“The Babcock appointment of KDC Veolia as the recycler for Swiftsure marks a significant strategic milestone in the UK Submarine Dismantling Project. As the demonstrator for the project, Swiftsure will be the first UK nuclear powered submarine to be dismantled. Lessons learned will be applied to improve the process for dismantling of all future submarines, ensuring all boats can be safely and efficiently recycled with cost savings where possible applied.” SDA CEO, Sir Chris Gardner KBE
– End –

Related Articles

UK CDS Underlines Importance of UK’s Nuclear Deterrent Effect on Russia

First steel cutting for Royal Navy’s fifth Type 26 frigate

Babcock bolsters South Korean relations to grow global opportunities
Life Unleashed: Solutions for a Balanced and Happy Existence
Inside Scoop: How Submarines Handle Food Scraps and Human Waste
Submarines are fascinating vessels that allow humans to explore the depths of the ocean. One aspect of submarine life that is often overlooked is how food scraps and human waste are managed in such an enclosed environment. In this article, we will delve into the various methods used by submarines to handle food scraps and human waste while remaining at sea for extended periods.
The Challenge of Managing Waste on Submarines
Living on a submarine presents unique challenges when it comes to waste management. With limited space and resources, submarine crews must carefully plan for the disposal of food scraps and human waste to maintain a hygienic and safe environment on board.
Food Waste Management
On a submarine, every scrap of food is precious. Submarine crews must carefully monitor their food consumption to minimize waste. Any leftover food scraps are collected and stored in designated containers to prevent any odors or contamination. These containers are tightly sealed to contain any smells and prevent attracting unwanted marine life.
Subheading: Food Waste Disposal
When it comes to disposing of food scraps, submarines have specific procedures in place. Depending on the submarine’s design, some may have food waste compactors that can reduce the volume of food scraps before disposal. The compacted waste is then stored in containers until it can be properly disposed of during designated waste disposal procedures. Other submarines may incinerate food waste to reduce the volume and minimize any potential odors.
Subheading: Waste Water Management
Submarines are also equipped with advanced waste water treatment systems to handle human waste. These systems are designed to treat and sanitize waste water before discharging it into the ocean. The treated water must meet stringent environmental regulations to ensure minimal impact on marine ecosystems.
Human Waste Management
Human waste on submarines is managed through a series of intricate systems designed to maintain hygiene and sanitation on board. Submarines are equipped with compact and efficient toilets that use vacuum technology to transport waste to storage tanks. These storage tanks are regularly emptied and sanitized to prevent any hygiene issues.
Subheading: Waste Water Treatment
Human waste is processed through a series of treatment systems on submarines. The waste water is first separated from solid waste and then undergoes a series of filtration and treatment processes to remove contaminants and pathogens. Once treated, the waste water is discharged into the sea following strict protocols to protect the marine environment.
Subheading: Contingency Plans
In the event of equipment failure or emergency situations, submarines have contingency plans in place to handle waste management. Crew members are trained to follow specific protocols to contain and manage waste effectively until normal operations can be resumed.
How do submarines prevent odors from food waste? Submarines use tightly sealed containers to store food scraps and may have compactors or incinerators to reduce waste volume and minimize odors.
How is human waste treated on submarines? Human waste on submarines goes through a series of treatment systems to separate solids and liquids, then undergoes filtration and treatment before being discharged into the ocean.
What happens in emergency waste management situations on submarines? Submarines have contingency plans in place for waste management in emergency situations, ensuring that waste is contained and managed effectively until normal operations can resume.
Do submarines follow environmental regulations for waste disposal? Submarines adhere to strict environmental regulations for waste disposal, ensuring that treated waste water meets stringent standards before being discharged into the ocean.
How do submarines ensure hygiene and sanitation with limited space for waste management? Submarines are equipped with compact toilets and waste storage tanks, along with advanced waste treatment systems, to maintain hygiene and sanitation on board.
In conclusion, submarines face unique challenges in managing food scraps and human waste while remaining at sea for extended periods. Through careful planning, advanced waste management systems, and adherence to environmental regulations, submarine crews can effectively handle waste on board and maintain a hygienic living environment. By understanding the intricate processes involved in waste management on submarines, we gain insight into the sustainable practices necessary to explore the ocean depths responsibly.
- High School
- You don't have any recent items yet.
- You don't have any courses yet.
- You don't have any books yet.
- You don't have any Studylists yet.
- Information
G10 Unit 9 P1 - G10 Unit 9 P1
English documents and practice, thpt nguyễn khuyến, preview text.
Full name. _______________________________ Newton Grammar School Class. ____________ English 10 Unit 9. PROTECTING THE ENVIRONMENT PRACTICE 1 Exercise 1. Circle the word which has underlined part pronounced differently.
A. effect B. emit C. establish D. export
A. use B. unit C. ugly D. union
A. preserve B. conserve C. fossil D. discuss
A. watch B. write C. woman D. white
A. species B. dresses C. beaches D. pages
A. finished B. isolated C. developed D. guessed
A. program B. borrowing C. government D. promotion
A. polar B. land C. impact D. animal
A. release B. easy C. threat D. increase
A. possession B. property C. access D. American Exercise 2. Circle the word which has a different stress pattern from the others.
A. improve B. toxic C. planet D. effort
A. plastic B. protect C. value D. landfill
A. dioxide B. organic C. utensil D. recommend
A. emission B. energy C. implement D. oxygen
A. eventually B. disposable C. category D. community
A. energy B. influence C. animal D. employment
A. carbon B. footprint C. hygiene D. resource
A. submarine B. assignment C. disposal D. depletion
A. local B. harmful C. healthy D. prevent
A. chemical B. solution C. disposal D. erosion Exercise 3. Choose the correct words to complete the sentences.
Schools are important in helping to raise environment/ environmental awareness.
The decline in the number of sharks is damaging the island's vulnerable environment/ ecosystem.
They use chemicals that will harm/ destroy the environment.
We must punish the companies that are polluting and damaging the nature/ environment.
The environmental impact/ preservation of the construction project is being considered.
The large amounts of CFC gases can cause the ozone pollution/ depletion.
Deforestation / Consumption has been shown to cause floods and drought.
A clear example can be seen in the case of the destruction of the ozone layer, causing the greenhouse effect/ gases.
The use of fossil fuels/ alternative energy can cause a lot of problems, but it is still essential in industry.
Polar ice heating/ melting can make the sea level rise, and many islands will disappear. Exercise 4. Choose the best option A, B, C or D.
There’s been a ______in Germany and a village was completely destroyed. A. flood B. drizzle C. shower D. smog
During the last hundred years we have done great ______to the environment. A. injury B. pollution C. damage D. hurt
There are lots of things we can all do to ______the environment. A. enhance B. protect C. make D. build
Environmentalists are furious with the American Government for delaying measures which will reduce greenhouse gas ______. A. exhaust fumes B. smokes C. wastes D. emissions
The government is introducing strict new rules on the dumping of ______by industry. A. pesticides B. exhaust fumes. C. toxic waste D. emissions
Thousands of acres of forest are being cut down every year and the ______of many animals are being destroyed. A. natural resources B. natural habitats C. ways of life D. living surroundings
Make sure your car runs on unleaded petrol and your home uses sources of ______energy. A. recycling B. reused C. renewable D. recyclable
Scientists have found holes in the ______, particularly over Antarctica. A. ice caps B. polar ice C. ozone layer D. greenhouse
If government don't ______global warming, more natural disasters will occur. A. achieve B. promote C. discourage D. prevent
Consumption of fossil fuels at an alarming rate can ______to global warming which can further result in melting of polar ice caps and increase in sea levels. A. lead B. drive C. attach D. run
Human activity is leading to the extinction of species and habitats and ____of bio- diversity. A. lose B. losing C. loss D. lost
"I'm a big fan of U23.” Derek said. => Derek said he ______a big fan of U23. A. was B. has been C. were D. had been
"We're watching TV," said the twins. => The twins said they ______TV. A. watched B. were watching C. have been watching D. had watched
“You've been annoying me all day!" my mum said. => My mum said I _____her all day. A. annoyed B. was annoying C. ‘ve been annoying D. had been annoying
"At one o'clock, I was having lunch," said Molly. Molly said she ______lunch at one o'clock. A. had been having B. has had C. is having D. has been having Exercise 5. Choose the answer which is CLOSEST in meaning to the underlined words.
Some of the waste materials can be reworked for reuse. A. redone B. recalled C. renewed D. preserved
The need to recycle water and other materials is obvious. A. doubtful B. hidden C. apparent D. ambiguous
Unless the oil spill is contained, irreparable damage will be done to the sea. A. rechargeable B. curable C. unfixable D. repairable
Helping to alleviate poverty also helps to reduce environmental destruction. A. enlarge B. enrich C. strengthen D. lessen
Increased consumption of water has led to rapid depletion of groundwater reserves. A. made up B. caused C. produce D. begin
We are facing severe environmental pollution despite the fact that many world organizations are working hard to reduce it. A. heavy B. destructive C. harmful D. serious Exercise 6. Choose the answer which is OPPOSITE in meaning to the underlined words.
Polluted water sources are a hazard to wildlife. A. security B. danger C. harmlessness D. safety
The case for better public transport is unanswerable. A. reliable B. believable C. answerable D. questionable
People should keep away from the radioactive waste. A. get along with B. keep in touch with C. put up with D. stay close to
Several outbreaks of infection have been traced to contaminated food. A. clean B. dirty C. polluted D. poisonous
Eat as many fresh products as possible rather than relying on tinned and packed foods. A. learning B. counting C. liberating D. depending
Fresh water is very important to life because no one can live without it. Yet it is one of the limited and most endangered natural resources on our planet. A. Clean B. Drinkable C. Polluted D. Running Exercise 7. Use the correct form of the words in brackets to finish the sentences.
Many species of animals are in danger of ________________ out. (DIE)
Mosquitoes are ________________ abundant in this dark wet place. (EXTREME)
________________, the museum was not damaged by the earthquake. (LUCK)
The more things a man is ashamed of, the more ________________ he is. (RESPECT)
The ________________ of the plant was the major blow to the local economy. (LOSE)
Noise has become one of the main ________________ of modern city life. (POLLUTE)
Different parts of the world have very different ______________ conditions. (CLIMATE)
They reported the _____________ of the bears to the missing animal bureau. (APPEAR)
Environmental __________ has increased dramatically over the past decades. (AWARE)
The threat of ________________ warming will force the world to cut down energy consumption. (GLOBE) Exercise 8. Choose the correct option.
She asked who I (am/ was) talking to.
He asked me why I (didn’t/ don’t) speak Japanese.
Johnny asked me where (did she live/ she lived).
Kimberly says that her brother (liked/ likes) roast beef.
Jennifer asked him what he (had been wanting/ had wanted) to do.
Ethan said, “They (had/ were) left the cafeteria when I came”
He said that he had visited Singapore (the month before/ a month ago).
He said that he (was/ is) going to resign then.
She said that she (had/ has) studied there for a long time.
He asked why (did he do/ he did) the household chores that day. Exercise 9. Choose the underlined words that need correction.
I asked her whether she would prefer to eat out or cooking a meal at home. A B C D
We are going to buy anything to eat because Tommy says he is hungry. A B C D
A. bear B. lay C. produce D. generate
A. though B. unless C. whether D. if
A. density B. environment C. habitats D. populations Exercise 11. Read the following passage and mark the letter A, B, C, or D to indicate the correct answer to each of the questions. THINK BEFORE YOU TOSS Countries around the world have growing mountains of trash because people are throwing out more trash than ever before. How did we become a throwaway society? First of all, it is now easier to replace an item than to spend time and money to repair it. Thanks to modern manufacturing and technology, companies are able to produce items quickly and inexpensively. Products are plentiful and prices are low, so we would rather buy something new than repair it. Even if we did want to repair something, many items are almost impossible to repair. These products contain many tiny, complicated parts. Some even contain small computer chips. It's easier to throw these items away and buy new ones than to fix them. Another contributing factor is our love of disposable products. As busy people, we are always looking for ways to save time and make our lives easier. Why should we use cloth kitchen towels? It's easier to use paper towel once and toss it out. Companies manufacture thousands of different kinds of disposable items: paper plates, plastic cups, cameras, and razors for shaving, to name a few. The problem is that disposable products also contribute to our trash problem. Our appetite for new products also contributes to the problem. We are addicted to buying things. As consumers, we want the latest clothes, the best TVs, and cellphones with west features. Companies tell us to buy, buy, and buy. Advertisements persuade us wer is better. The result is that we throw away useful possessions to make room for new ones.
Which of the following is NOT a reason for people to replace a broken item? A. Products are now mass produced at affordable prices. B. It takes almost no time to fix broken items. C. Many items are too complicated to repair. D. Some products contain tiny, complicated chips.
All of the following are disposable products, EXCEPT ____. A. cloth kitchen towels B. paper plates C. plastic cups D. razors for shaving
The word “disposable" in paragraph 3 is closest in meaning to ____. A. convenient B. inexpensive C. throwaway D. single-use
Why are we hooked on buying new things? A. We throw the old items to make room for the new ones. B. We have more money than ever before. C. We want to own as many things as possible. D. We are made to believe that the new is the better.
The word “appetite” in the last paragraph can be best replaced by ____. A. need B. demand C. desire D. taste Exercise 12. Read the passage and choose the correct answer to complete blanks. Ozone is a gas made up of molecules that are formed by three oxygen atoms. (1) ______ is O3. Ozone is formed when the sunlight hits oxygen molecules (O2) and (2) ______ into individual atoms. These individual atoms then join up with O2 molecules and make O3, or ozone. Way up high in the Earth’s atmosphere, called the stratosphere, there is (3) ______ of ozone molecules that are formed when the sun hits oxygen molecules. (4) ________. Ozone molecules in the atmosphere provide us with important protection from the rays of the sun. Specifically, these molecules are good at absorbing certain ultraviolet rays that can cause (5) _____ and skin cancer. It turns out that certain types of molecules can cause a chemical reaction (6) ______. This cause the ozone to break up and become unable to absorb ultraviolet light. The main molecules that are destroying the ozone layer are called chlorofluorocarbons or CFCs.
A. This molecule formula B. Its molecule formula C. Their molecule formula D. That molecule formula
A. breaks them up B. to break them up C. breaking them up D. break them up
A. a fair high concentrate B. a fairly highly concentrate C. a fairly high concentration D. a fair highly concentration
A. This part of the atmosphere which is called the ozone layer B. Being called the ozone layer is this part of the atmospher C. This part of the atmosphere is called the ozone layer D. This part of the atmosphere to be called the ozone layer
A. sunburned B. sunburnt C. sunburning D. sunburn
A. during they come in contact with ozone molecules B. when to come in contact with ozone molecules C. once they come in contact with ozone molecules D. since coming in contact with ozone molecules
- Multiple Choice
Subject : English Documents and practice
School : thpt nguyễn khuyến.


COMMENTS
The cans are ejected from the submarine using a trash disposal unit (TDU), which is a long cylindrical, vertical tube connected to the ocean through a ball valve. Several cans are placed atop one another in the TDU, the top of the TDU is sealed by closing a pressure cap, the ball valve is opened, and the cans ejected through a combination of ...
X-Post: "TIL how trash is disposed of in modern large submarines. Trash is deposited into a Trash Disposal Unit (TDU) which collects and compacts it into a galvanized steel can. A ball valve is opened allowing the scrap iron-weighted can to fall down to the sea floor."
goods. Recycling leaves and grass, for instance, is a great way to make compost. (9) ____ homemade. compost is obviously a lot cheaper than buying compost and this is a useful way to save money. Saving. money through recycling ultimately helps the environment. Recycling is just one of many ways that we can help the environment.
Submarine Reactor Plants (USN 1984) and updated and expanded in the Final Environmental Impact Statement on the Disposal of Decommissioned, Defueled Cruiser, Ohio Class, and Los Angeles Class Naval Reactor Plants (USN 1996). In USN 1984 and 1996, the Navy evaluated many options for the disposal of reactor plants from various nuclear powered ...
The following paper ls an excerpt from the booklet U.S. Naval Nuclear Powered Submarine Inactivation.Disposal. and Recycling published In March of 1995 by the Sea Systems Command of the U.S. Navy. 1he information from that publication is reprinted in response to several requests for the rest of the story following Mr. Bill Galvani's article Mooring ALPBA-End of the line in the October 1997 ...
Babcock Chief Executive, Nuclear, Harry Holt, said: "This is a world first. We are bringing together our experience of supporting the entire UK submarine fleet, our nuclear expertise and our ability to bring the best of industry together on this programme to spearhead the approach for the safe disposal of all ex-service nuclear submarines."
The Ship-Submarine Recycling Program (SRP) is the process that the United States Navy uses to dispose of decommissioned nuclear vessels. SRP takes place only at the Puget Sound Naval Shipyard (PSNS) in Bremerton, Washington, but the preparations can begin elsewhere. Program overview
Living on a submarine presents unique challenges when it comes to waste management. With limited space and resources, submarine crews must carefully plan for the disposal of food scraps and human waste to maintain a hygienic and safe environment on board. Food Waste Management. On a submarine, every scrap of food is precious.
Enlisted Designator 1 (Divers, Explosive Ordnance Disposal, Sea-Air-Land, Career Recruiter, etc.) must submit NAVPERS 1306/7 ... Request for assignment of submarine specific NEC. See MILPERSMAN 1306-416 for amplifying instructions on how to apply for submarine reinstatement. 1306-406 CH-19, 12 Apr 2007 Page 2 of 3
A. submarine B. assignment C. disposal D. depletion. A. local B. harmful C. healthy D. prevent. A. chemical B. solution C. disposal D. erosion Exercise 3. Choose the correct words to complete the sentences. Schools are important in helping to raise environment/ environmental awareness.