

9 Real-Life Lean Manufacturing Examples
Lean manufacturing allows companies to better optimize processes, reduce waste, and speed up production times through different methods, tools, and philosophies. If you're wondering how to implement lean manufacturing techniques in your operations, you need to consider which lean production tools you use and what you want to accomplish.
How Does Lean Manufacturing Work?
Lean manufacturing is a systematic approach to improving efficiency and reducing waste in manufacturing processes. It focuses on creating more value for customers while using fewer resources. This is achieved by identifying and eliminating all types of waste, including defects, overproduction, waiting, unnecessary motion, excess inventory, overprocessing, and unused talent. Lean manufacturing also emphasizes continuous improvement, involving all employees in the process of identifying and solving problems. By applying lean principles, companies can reduce lead times, improve quality, increase productivity, and lower costs.
Why Is Lean Manufacturing Important and How Can It Help?
Lean manufacturing is important because it helps companies stay competitive in today's fast-paced and ever-changing business environment. By improving efficiency and reducing waste, companies can offer better products and services at lower costs, which can attract and retain customers. Lean manufacturing can also help companies reduce their environmental impact by minimizing resource consumption and waste generation. Moreover, lean manufacturing can improve employee morale and engagement by empowering them to participate in continuous improvement activities and take ownership of their work. Overall, lean manufacturing can help companies achieve long-term success by creating value for customers, employees, and stakeholders.
Getting Started with Lean Manufacturing Methods
A great way to start considering methods is by exploring real-life examples of lean manufacturing and lean management. This can provide a deeper level of understanding and help you build up the confidence to implement the same lean thinking philosophies. We've compiled a list of nine examples for you to start with.
9 Lean Manufacturing Examples in the Real World
Kaizen is a Japanese term that means "continuous improvement." In the context of lean manufacturing, it refers to the idea of involving all employees in identifying and implementing small, incremental improvements in processes, products, or services. Kaizen encourages continuous learning and innovation , as well as a sense of ownership and engagement among employees. Some examples of kaizen activities include participating in quality circles, conducting 5S audits, or attending training sessions to learn new skills or techniques.
2. Just-in-time
Just-in-time (JIT) is a manufacturing philosophy that aims to produce only what is needed, when it is needed, and in the exact quantity needed. JIT helps companies minimize inventory and reduce waste, while also improving efficiency and responsiveness to customer demand. Some examples of JIT in action include using pull production systems, where production is triggered by customer orders rather than a forecast, or establishing close relationships with suppliers to ensure the timely delivery of materials.
Kanban is a visual tool that helps companies manage inventory and production by signaling when it is time to replenish supplies or move materials to the next stage of production. Kanban can take many forms, such as colored cards, electronic displays, or physical containers. By using kanban, companies can improve communication and coordination between different departments or functions, as well as reduce lead times and minimize waste.
4. Standardization
Standardization refers to the process of creating and implementing standard operating procedures (SOPs) for a given process or task. SOPs help ensure consistency and quality in products or services, as well as reduce variability and errors. Standardized work instructions can include visual aids, such as diagrams and photos, to help workers understand the process, and they can be updated as improvements are made. For example, standardization can be applied to the layout and design of the factory floor. The location of tools and equipment can be standardized so that workers can quickly find what they need, reducing wasted time and motion. The use of color-coded labels and markings can also help ensure that workers can quickly identify different parts and materials, reducing the risk of errors and accidents.
5. Value stream mapping
Value stream mapping is a tool used to visualize and analyze the flow of materials, information, and activities required to deliver a product or service to a customer. Value stream mapping helps companies identify and eliminate waste, as well as optimize the entire value stream from end to end. Value stream mapping can also reveal opportunities for improvement and innovation, such as reducing lead times, improving quality, or increasing flexibility.
6. Pull production
Pull production is a manufacturing approach where production is triggered by customer demand, rather than a forecast or a push from upstream processes. Pull production helps companies reduce inventory, improve responsiveness to customer demand, and minimize waste. Pull production can take many forms, such as kanban systems, supermarkets, or direct customer orders.
5S is a workplace organization and cleanliness system that helps companies improve safety, efficiency, and quality. The five S's stand for Sort, Straighten, Sweep, Standardize, and Sustain.
Sort refers to the process of separating necessary items from unnecessary ones and disposing of the latter. Straighten refers to the process of organizing the workplace and arranging items in a logical and efficient manner. Sweep refers to the process of cleaning and maintaining the workplace to ensure safety and hygiene. Standardize refers to the process of establishing and maintaining standards for workplace organization and cleanliness. Sustain refers to the process of continuously improving and refining the 5S system.
One of the most powerful lean manufacturing tools available to manufacturers is the SMED event . In a nutshell, SMED events enable manufacturers to identify—and remove—the waste in their changeover processes. All manufacturers, regardless of size, can benefit from SMED. Typically, SMED events reduce changeover times by 30-50%!
Steps include mapping your current changeover process; analyzing, extracting, and streamlining steps; and documenting the whole process to present to your organization.
9. Continuous flow
Continuous flow is a manufacturing approach that aims to produce products in a continuous and uninterrupted flow, rather than in batches. This approach helps companies minimize inventory, reduce lead times, and improve efficiency by eliminating waiting times and reducing the need for transportation and handling. Continuous flow is often used in industries such as food processing, pharmaceuticals, and electronics, where high levels of quality and consistency are required, and where the cost of errors or defects is high. Some examples of continuous flow in action include assembly line production, where each worker performs a specific task in a sequential manner, or cellular manufacturing, where groups of machines and workers are organized in a flow line to produce a family of related products.
Major Companies That Exemplify Lean Management Practices
You can’t talk about lean manufacturing without talking about Toyota. This Japanese auto manufacturer is credited with the birth of the Toyota Production System (TPS) . Created by Sakichi Toyoda, the goal of TPS was to eliminate waste from the manufacturing process. Nowadays, TPS is known as a fundamental lean manufacturing methodology. But Toyota didn’t stop at TPS. They also used a methodology called jidoka to minimize faulty products, and kaizen to pursue continuous improvement. They focused on automating several processes to lower human error and recheck product quality. Then, they implemented the just-in-time (JIT) model, so that they would only begin working on a product when there was a demand for it. This helped them to better control inventory levels and prevented overproduction.

FedEx Express
In response to the 2008 recession, FedEx began implementing lean manufacturing strategies to reduce costs. One of the ways they changed their operations was by introducing milestones in their C-check process for aircraft maintenance. The team identified 68 milestones crucial to the C-check and defined each segment in 4-hour increments. Identifying milestones enabled a smoother workflow, which greatly reduced wasted time. The FedEx Express crew at LAX went from performing 14 C-checks a year to performing 30 a year. The crew also went from needing 32,715 man-hours for a C-check to 21,535 (and decreasing). Eliminating wasted time like this leads to huge cost savings, especially in an industry like aircraft maintenance, where specialized mechanics and technicians are quite costly.
With almost 800 contracted factories involved in their manufacturing processes, it’s no surprise that Nike places a heavy emphasis on consistency and waste reduction. To do so, Nike adopted continuous improvement practices and developed the Manufacturing Index in 2011: a framework with key benchmarks and performance indicators to reduce miscommunications, waste, and inconsistency across manufacturers. The index contains lean elements like “just-in-time” and a continuous improvement mindset. Just-in-time (JIT) production is a simple inventory system where you only produce if there is a demand for your production. This is the pillar of the TPS principles. By not having excess inventory lying around, you reduce waste and save space.
Harley-Davidson
Harley-Davidson used Total Productive Maintenance (TPM) along with the 5S system and Standard Work as the main foundations of their strategy to keep their techniques stable. Then, they added other lean tools—such as kaizen and Six Sigma—to help improve operations and problem-solve issues. The company also adopted just-in-time inventory management and value stream mapping. The result? Having exactly the right inventory levels at the right times, avoiding waste and providing value to their customers. With these tools, Harley-Davidson automated processes to increase productivity, improve lead times, and reduce their transportation expenses.
John Deere Production System
John Deere started their lean thinking with production processes before moving on to improving their logistics and their supply chain. For John Deere, adopting continuous improvement processes took the form of automated quality control mechanisms. These mechanisms could check more products in less time, allowing for workers to spot defects — and subsequently fix them — more quickly. They were also able to get more products out the door and into customers' hands.
Kimberly-Clark
Kimberly-Clark felt that they were overspending on their transportation management system (TMS). Kimberly-Clark sought continuous improvement to further automate the system, which freed up more time for analysts to perform proactive work that benefited the company. The automation also allowed them to perform more processes with less clicks and fewer steps within the application.
Intel’s components have to be produced with the highest quality—and meet extremely high customer demand. With such demand, Intel could have lowered their cycle time to increase output, but that would have resulted in poorer quality and increased the chance of product defects. Instead, the semiconductor company turned to lean techniques to reduce works-in-process (WIP) and get rid of process waste without hindering workflow. Then, they implemented quality control methods. These lean tools helped to boost productivity without sacrificing quality for their products.
The Ford Motor Company has always aimed to produce the highest quality products and innovations in the industry. Knowing that its operational strength lay in its assembly line, Ford adopted kaizen, lean manufacturing methodologies , Six Sigma, and Total Quality Management (TQM) to implement the concept of continuous improvement in their processes. Adopting automation and standardization allowed the company to create production lines that flowed efficiently as products moved through each workstation. Using these methods, Ford improved product quality, reduced costs, and decreased waste.
Bank of America
Bank of America is one of many financial institutions that apply a hybrid of lean manufacturing principles and Six Sigma to their operations. Before employing these principles, the organization was experiencing low customer satisfaction rates due to their process quality. They had many issues with customers' statements including encoding errors, late posting transactions, and omissions. With lean Six Sigma, they improved operational efficiency while meeting the customer needs. They also managed to continuously assess performance using the right performance data metrics to ensure optimized processes.
General Electric
General Electric (GE) recently took on lean management t with the arrival of their new CEO and chairman in 2018. When the company first adopted lean techniques in their project management operations, their innovations actually created bottlenecks in other processes. This led to too much downtime and inventory, which in turn created more waste. To correct this, GE’s management team turned to Genba. Genba is a lean manufacturing too l used to evaluate the processes on the work floor and learn more about the issues. They sent work operators and support team members to obtain lean training, then performed value stream mapping to identify process value and potential areas of waste. After changing tactics, they were able to correct their first pass at employing lean strategies.
Improve Your Factory with Lean Manufacturing Tools Like Amper
Implementing lean manufacturing principles and lean tools often requires the help of software. Trying to manually track, monitor, and organize the different steps of a lean process is overwhelming and can easily lead to errors and slowdowns. However, with the help of technology like production monitoring, machine monitoring, and IoT and cloud computing, you can track the waste and value in all of your manufacturing systems and develop better ways to reduce waste and increase profitability.
You can apply lean manufacturing to your operations in a vast number of ways. The nine case studies above show that with the right lean tools and techniques, it’s possible to overhaul systems, equipment, production lines, and worker output to continually improve operations. These are just a few success stories within their industries that can inspire other manufacturers to pursue similar tactics. Here at Amper, we offer OEE and machine monitoring to further automate and enhance lean manufacturing system strategies that you adopt within your operations. Contact us to learn more about our tools and resources, or schedule a demo today!
Recent blogs
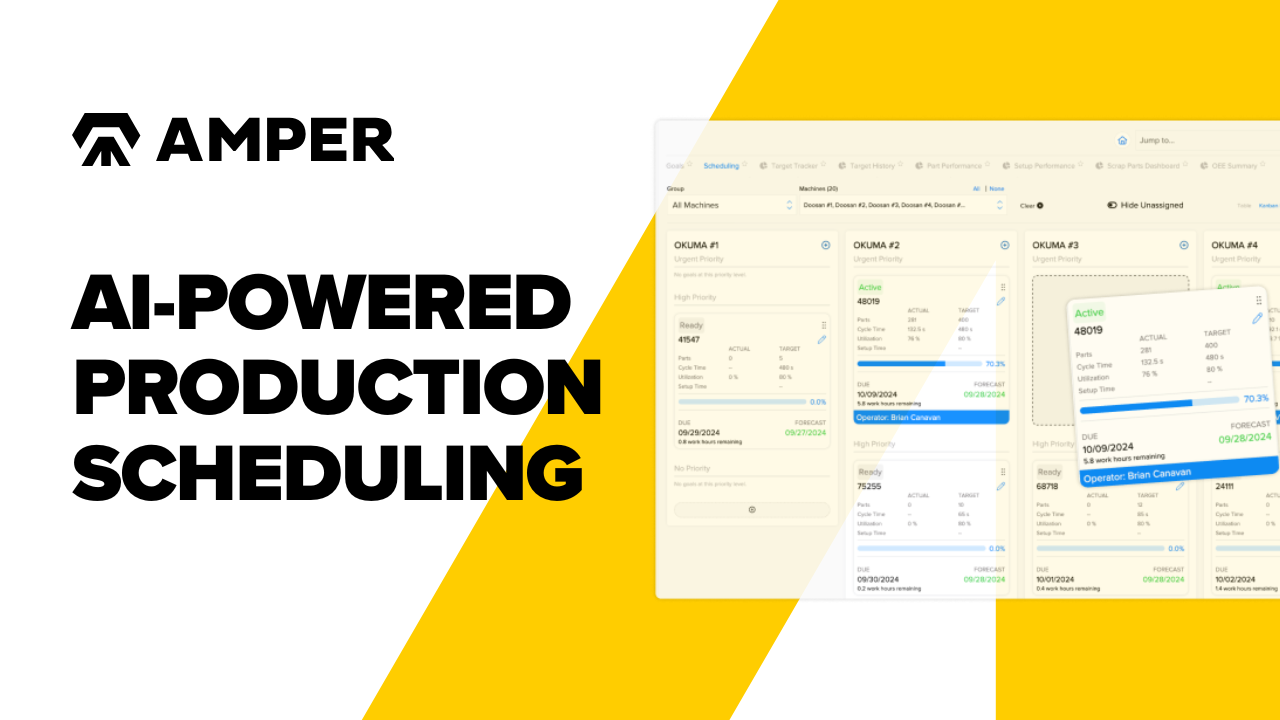
How to use AI-powered production planning and scheduling
.png)
Amper named Hendrick Motorsports' official MES partner
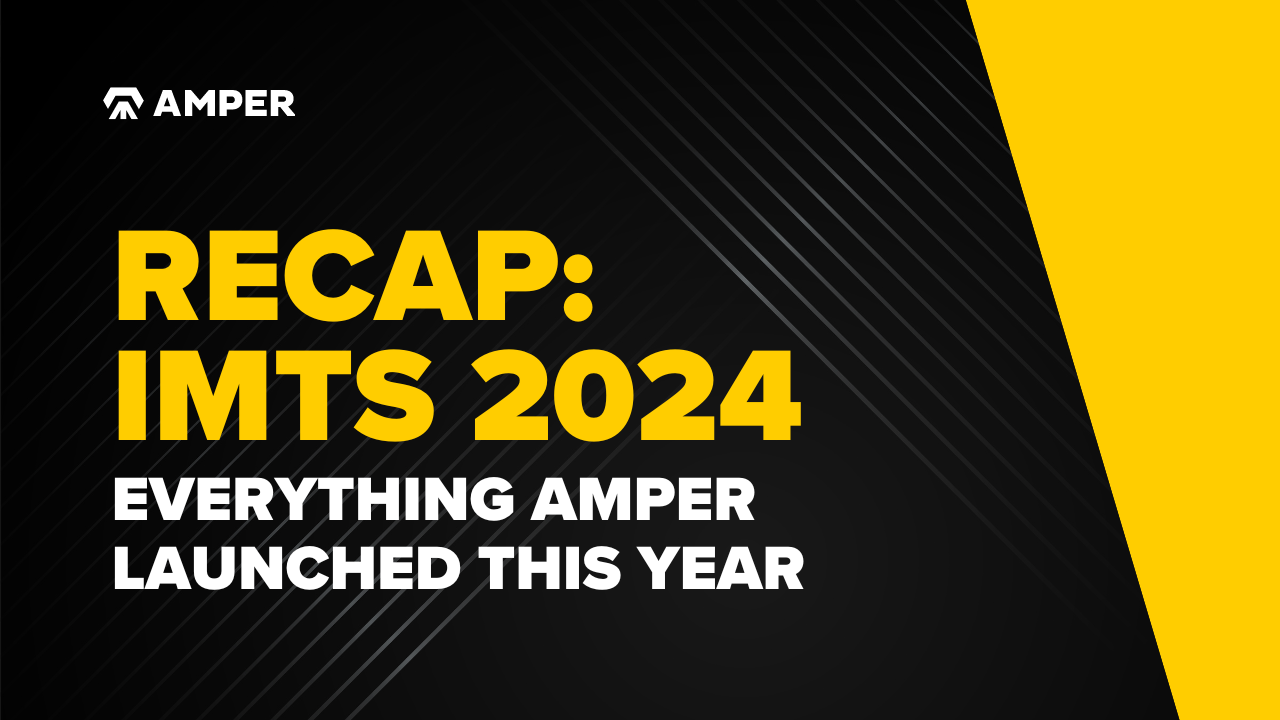
IMTS 2024 Recap
770 N Halsted St. #308 Chicago, IL 60642

IMAGES
VIDEO